The integration of laser welding and advanced technologies has revolutionized precision in manufacturing and welding processes. Manufacturers can achieve unparalleled accuracy, efficiency, and quality control by combining the precision and versatility of laser welding with other cutting-edge technologies.
The topic explores these possibilities and the benefits of integrating laser welding with these advanced technologies, driving advancements in precision engineering and redefining the options in modern manufacturing.
1. CNC Laser Beam Welding (Combining Laser Beam Welding and CNC Technology)
CNC laser beam welding combines the precision of laser beam welding with the automated control of CNC technology, offering a powerful solution for precise, efficient welding operations. These integrated systems provide accurate control over the laser beam, ensuring precise welds on various materials.
However, it’s crucial to outsource to a reliable company that offers high-standard laser welding services, prioritizing delivering exceptional quality and meeting stringent industry standards.
CNC programming enables the creation of complex welding patterns and designs, while real-time monitoring systems ensure weld quality and consistency. With the versatility and precision of micro laser welding combined with the automation and control of CNC technology, CNC laser beam welding is an ideal choice for industries seeking reliable and high-quality welding solutions.
2. Laser Welding and 3D Additive Manufacturing Technology
Laser welding and 3D additive manufacturing technology combine the precision of laser welding with the versatility of 3D printing. The integration allows for creating of complex, three-dimensional objects by selectively melting and fusing metal powders layer by layer. The applications of this technology span various industries, including aerospace, automotive, healthcare, and jewelry design.
Examples include producing lightweight aerospace components, custom medical implants, intricate jewelry designs, and prototyping. Due to the critical nature of weld quality and material integrity, the successful implementation of laser welding and 3D additive manufacturing requires the expertise of a reliable welding company, like Micro Weld, Inc, with experience in this specialized field.
3. Laser Welding and 4.0 Technologies
Laser welding and 4.0 technologies integration represent a significant advancement in industrial manufacturing. Manufacturers can achieve enhanced productivity, quality control, and efficiency by combining laser welding with Industry 4.0 technologies like IoT, big data analytics, automation, and artificial intelligence. IoT connectivity enables real-time monitoring and data exchange, optimizing welding processes and facilitating predictive maintenance.
Big data analytics and AI algorithms offer process optimization and defect detection insights. Automation and robotics enable the seamless integration of laser welding into production lines.
This integration empowers manufacturers to harness the full potential of laser welding while embracing the transformative capabilities of Industry 4.0 for smart and interconnected manufacturing systems.
4. Laser Welding and Weld Monitoring Systems
Integrating laser welding and weld monitoring systems involves combining laser welding technology with advanced monitoring systems, which helps enhance the quality control and efficiency of welding processes.
These systems utilize sensors, cameras, and data analysis techniques to monitor critical parameters during weldings, such as temperature, weld penetration, and weld quality. Real-time monitoring immediately detects defects or deviations, enabling timely adjustments and ensuring consistent weld quality.
The integration is crucial in industries requiring critical weld integrity, such as automotive, aerospace, and pipeline manufacturing. Continuous monitoring ensures the highest standards of weld integrity and product reliability. Partnering with a reliable welding company that offers integrated weld monitoring systems like Micro Weld, Inc, is vital to achieving optimal results and ensuring the highest quality welds.
5. Robotic Laser Welding (Combining Robotics and Laser Beam Welding)
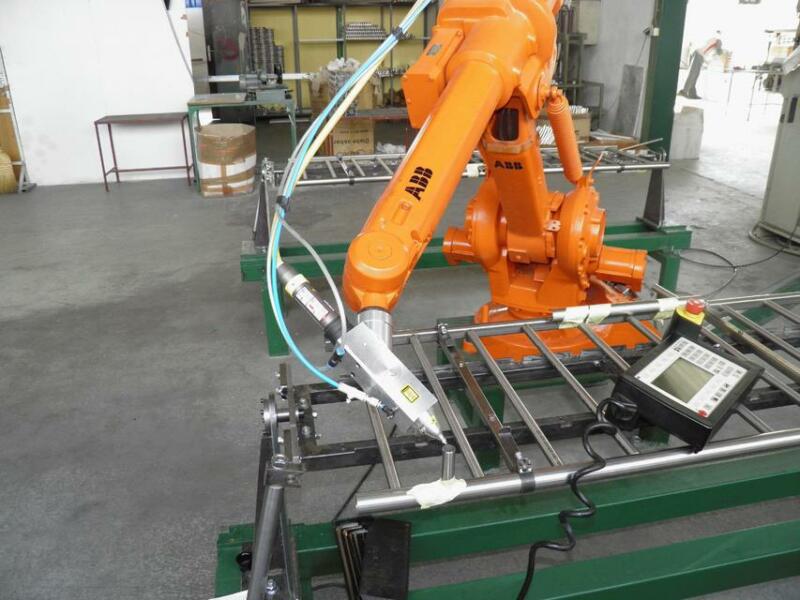
Robotic laser welding is a powerful integration of robotics and laser beam welding technologies. The approach utilizes industrial robots with laser welding capabilities to perform precise, automated welding operations. The robots are programmed to accurately manipulate the laser beam, enabling consistent and repeatable welds on various materials.
The integration offers numerous advantages, including increased production speed, improved weld quality, and enhanced worker safety by reducing manual intervention. Robotic laser welding finds applications in automotive manufacturing, aerospace fabrication, and other industries where high-volume production and stringent quality standards are paramount. Leveraging the expertise of a reliable welding company is crucial for the successful implementation and optimization of robotic laser welding systems.
6. Integration of Laser Beam Welding Technology With Augmented Reality
Integrating laser beam welding technology with augmented reality (AR) is a cutting-edge development in industrial manufacturing. By combining these technologies, manufacturers can enhance precision, efficiency, and quality control in welding processes. Augmented reality overlays digital information onto the real-world environment, providing operators with real-time visual guidance and data during welding operations.
The integration lets providers of laser welding services visualize weld paths, joint positions, and welding parameters, improving accuracy and reducing errors. AR also facilitates weld inspection and quality control by overlaying digital inspection data onto welded surfaces. Integrating laser beam welding with augmented reality holds significant potential for industries seeking to optimize welding processes and improve overall productivity.
However, collaborating with a trusted welding company like Micro Weld, Inc is crucial to leverage the full potential of the integration and maximize the benefits of combining laser beam welding technology with augmented reality in industrial manufacturing.
7. Magnification and Laser Welding
Magnification plays a crucial role in laser welding, enhancing precision and control during the welding process. By using magnification techniques, such as microscopes or optical systems, welders can closely examine the weld joint, ensuring accurate alignment and monitoring of the weld pool dynamics. Magnification allows for better visualization of the welding zone, enabling welders to make precise adjustments and achieve high-quality welds.
It’s particularly beneficial when working with small or intricate components that require meticulous attention to detail. Integrating magnification with laser welding improves weld quality, reduces errors, and enhances overall welding performance, making it an essential tool in various industries, including electronics, medical devices, and jewelry manufacturing.
Conclusion
Integrating laser welding with advanced technologies is driving the advancement of precision in manufacturing and welding processes. Manufacturers can achieve unparalleled accuracy, efficiency, and quality control by combining laser welding with CNC, 3D additive manufacturing, augmented reality, and other cutting-edge technologies.
By harnessing the power of laser welding and advanced technologies, manufacturers can push the boundaries of precision engineering, achieve intricate designs, and meet the demands of diverse industries such as aerospace, automotive, medical, and jewelry. However, outsourcing to a reputable welding company like Micro Weld, Inc is fundamental to leveraging these advancements fully while maintaining high standards of quality and reliability.
Also read: The Basics of Sheet Metal Fabrication: Techniques, Applications, and Benefits